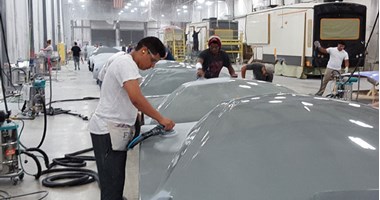
Comment créer un environnement de travail idéal - 101.
Un espace de travail bien aménagé est la clé de la productivité quotidienne. La façon dont vous aménagez votre environnement de production a une incidence directe sur la qualité des produits, la sécurité, la durée de vie des outils et l'efficacité globale. Découvrez-en plus à ce sujet dans cet article de blog.
L'aménagement d'un lieu de travail idéal déterminera la manière dont tout le reste se déroulera au cours des routines de production quotidiennes. Garantir un produit de bonne qualité, un environnement de travail sûr, une durée de vie plus longue des outils, réduire les coûts de réparation et d'énergie et augmenter la productivité est étroitement lié à la manière dont vous configurez votre production dès le départ.
Étape 1 : Régler correctement le système d'alimentation en air
Pour concevoir une installation optimisée et tournée vers l'avenir, la précision est essentielle. Commencez par définir clairement la consommation totale d'air, en tenant compte à la fois des besoins actuels et du potentiel de croissance future, tout en prévoyant une marge de sécurité.
Tenez compte des spécificités de chaque zone opérationnelle, en positionnant stratégiquement les sorties d'air en fonction des espaces de travail ou des cellules désignés.
Pour affiner les performances, examinez les besoins en volume d'air de chaque outil ou cellule. Choisissez soigneusement les tuyaux d'air et les bouchons, en tenant compte de facteurs tels que le diamètre interne, la longueur et la compatibilité structurelle.
Plus d'informations sur Dynabrade FRL ici
Améliorez la fiabilité de l'ensemble du système en intégrant un système de filtre/régulateur/lubrificateur (FRL), qui non seulement assure une qualité d'air irréprochable, mais maintient également une pression et une lubrification optimales dans la mesure du possible.
Si l'utilisation d'un graisseur est impossible, la lacune doit être comblée par une solution pratique : le graissage manuel entre les équipes.
Cette approche holistique permet non seulement de préparer l'installation à des opérations quotidiennes fluides, mais souligne également un engagement en faveur de l'efficacité et de l'excellence durables, ouvrant la voie à un espace de travail performant et prêt pour l'avenir.
Étape 2 : Optimiser la qualité de l'air dans la zone de travail
L'amélioration de la qualité de l'air dans la zone de travail exige une approche stratégique et proactive.
Les pratiques optimales commencent par l'utilisation d'outils compatibles avec l'aspiration, équipés de plateaux de ponçage et d'abrasifs perforés pour extraire la poussière à la source.
Cela contribue non seulement à un environnement de travail plus sain, mais minimise également les efforts de nettoyage et réduit la dépendance à l'égard d'accessoires supplémentaires d'équipement de protection individuelle (EPI).
Pour renforcer ces efforts, envisagez une analyse complète des risques. Faites appel à l'expertise d'un tiers éligible ou travaillez avec votre service interne de santé, de sécurité et d'environnement (SSE) pour réaliser une évaluation approfondie.
Cette analyse a pour but d'identifier toutes les zones de danger potentiel au sein de votre établissement et de fournir une feuille de route pour des interventions ciblées et des stratégies d'atténuation des risques.
En outre, lorsqu'il s'agit de réduire le risque d'inflammation et d'explosions potentielles, l'intégration d'un extracteur approprié certifié Ex devient primordiale.
Cette mesure s'aligne non seulement sur les normes de sécurité, mais sert également de mesure préventive solide, garantissant le bien-être de la main-d'œuvre et de l'établissement dans son ensemble.
En adoptant ces mesures, l'engagement en faveur d'un environnement de travail plus sûr, plus sain et plus efficace occupe le devant de la scène.
Étape 3 : Appliquer des mesures de maintenance préventive
Le maintien d'une efficacité opérationnelle maximale dépend des mesures de maintenance préventive.
En plus des procédures de lubrification à l'air décrites ci-dessus, il est impératif de suivre les directives du fabricant pour les outils à engrenages planétaires, en appliquant de la graisse, et pour les outils à angle droit sans système de mèche', en utilisant de l'huile pour engrenages selon les instructions.
Cette approche méticuleuse permet non seulement de garantir des performances optimales, mais aussi de prolonger la durée de vie des composants essentiels.
Évitez les problèmes potentiels en empêchant les entrées d'air des outils d'être exposées à la poussière lorsqu'elles ne sont pas raccordées à un tuyau d'air. L'air sous pression, s'il n'est pas contrôlé, peut pousser les particules de poussière dans le moteur pneumatique, menaçant l'intégrité des pièces rotatives.
Inspectez et surveillez régulièrement les pourcentages d'usure des composants en fonction des directives du fabricant et corrigez l'usure de manière préventive afin d'éviter les temps d'arrêt.
Envisagez de renforcer votre résilience opérationnelle en conservant un stock de moteurs de rechange ou de kits de mise au point. Ce stock stratégique agit comme une sécurité intégrée, garantissant le fonctionnement ininterrompu de l'outil et minimisant les temps d'arrêt potentiels.
Pour les réparations internes, suivez les recommandations du fabricant en utilisant des outils de réparation d'origine spécialement conçus, en accordant une attention méticuleuse aux instructions d'assemblage, aux valeurs de couple et aux adhésifs spécifiés afin de garantir un remontage précis et fiable.
Pour la sécurité et la longévité de l'outil, utilisez toujours les abrasifs et les accessoires recommandés par le fabricant.
Cela permet non seulement de prévenir les accidents sur le lieu de travail, mais aussi d'éviter les risques de maladies professionnelles, les vibrations excessives et les défaillances prématurées des outils. En adoptant ces mesures préventives, votre stratégie de maintenance devient la pierre angulaire d'une productivité soutenue et de l'excellence opérationnelle.
Étape 4 : Définir des mesures de santé et de sécurité
Outre les questions de santé, de sécurité et d'environnement (SSE) mentionnées ci-dessus, un certain nombre d'autres facteurs clés jouent un rôle décisif dans le maintien d'un environnement de travail sûr et efficace.
Il est primordial de sélectionner correctement les accessoires abrasifs, notamment en fonction de la vitesse de rotation des outils et des abrasifs.
Veiller à ce que la vitesse maximale de fonctionnement (MOS) de l'outil ne dépasse jamais la vitesse maximale de fonctionnement (MOS) de l'accessoire abrasif est essentiel pour la performance et la sécurité.
Dans les environnements sujets à de fréquentes décharges électrostatiques, il est fortement recommandé d'adopter un outil de détection des décharges électrostatiques (ESD), ainsi qu'un tuyau conducteur et un système d'aspiration. Cela permet non seulement de protéger les opérateurs contre les petits chocs, mais aussi de protéger les équipements électroniques et de réduire le risque d'explosions potentielles au sein de l'installation.
Découvrez tous les outils ESD de Dynabrade ici
Une pratique indispensable pour tous les opérateurs est la lecture approfondie et la compréhension du manuel d'utilisation avant la première utilisation de l'outil.
En outre, il est essentiel d'inspecter les accessoires abrasifs avant leur utilisation afin de détecter tout dommage structurel, ce qui renforce la fiabilité et la sécurité.
L'utilisation de l'équipement de protection individuelle (EPI) nécessaire n'est pas négociable, car il constitue une défense de première ligne contre les risques potentiels.
Enfin, évitez de stocker des produits chimiques dans ou autour de la zone de travail, afin de minimiser le risque d'interactions involontaires et de garantir un espace de travail sûr et bien défini.
En adoptant ces mesures, le lieu de travail devient non seulement plus sûr, mais favorise également une culture de la responsabilité et de la sensibilisation parmi les opérateurs.
Conclusion
La qualité de l'air, tant celle de l'environnement de travail que celle de l'air sous pression fourni aux outils, est cruciale pour la longévité des deux ressources les plus importantes de l'entreprise : son personnel et son équipement, qui lui permettent de fabriquer des produits de qualité et de valeur. En tant que Dynabrade, nous pouvons vous aider à améliorer ces deux éléments pour atteindre un niveau de classe mondiale. La maintenance préventive et les mesures HSE contribuent également fortement à la durabilité d'une bonne installation à long terme.